KCS 표준시방서 243115 알루미늄구조(한계상태설계법)
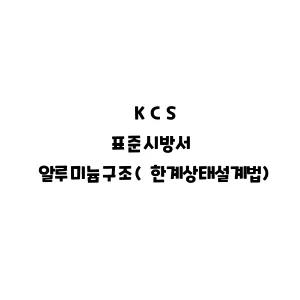
알루미늄 구조물 시방서
1. 일반사항
1.1 적용범위
- 이 기준에 기재하지 않은 사항은 당해 공사의 공사시방서에 따른다.
1.2 참고 기준
1.2.1 관련 법규
- 내용 없음
1.2.2 관련 기준
- KS B 0802 금속 재료 인장 시험 방법
- KS B 0886 알루미늄 용접 기술검정에 있어서의 시험방법 및 판정기준
- KS B 0897 알루미늄 맞대기 용접부의 초음파 경사각 탐상 시험방법
- KS B 1002 6각 볼트
- KS B 1010 마찰접합용 고장력 6각볼트, 6각너트, 평와셔의 세트
- KS B 1012 6각 너트
- KS B 1016 기초볼트
- KS B 1017 접시 머리 볼트
- KS B 1326 평와셔
- KS B 2819 토크-전단형 고장력 볼트․6각너트․평와셔의 세트
- KS B 5209 강제 줄자
- KS B 5221 미터 보통 나사용 한계 게이지
- KS B 14731 용접 업무 조절-임무와 책임
- KS B ISO 273 볼트 구멍 및 카운터 보어지름
- KS B ISO 1234 분할 핀
- KS B ISO 2338 평행 핀
- KS B ISO 2339 비경화 테이퍼 핀
- KS B ISO 3269 파스너-인수 검사
- KS D 0242 알루미늄 평판 접합 용접부의 방사선 투과 시험 방법
- KS D 0544 알루미늄 및 알루미늄합금 용접부의 초음파 탐상 시험의 기술 검정에서의 시험 방법 및 판정 기준
- KS D 1851 알루미늄 및 알루미늄 합금 분석 방법 통칙
- KS D 1869 알루미늄 및 알루미늄합금의 아연 분석 방법
- KS D 6008 알루미늄 주물
- KS D 3862 도장 용융 55% 알루미늄-아연 합금도금 강판 및 강대
- KS D 6701 알루미늄 및 알루미늄 합금의 판 및 띠
- KS D 6705 알루미늄 및 알루미늄합금 박
- KS D 6711 알루미늄 및 알루미늄 합금의 도장판 및 띠
- KS D 6713 알루미늄 및 알루미늄 합금 용접관
- KS D 6759 알루미늄 및 알루미늄합금 압출 형재
- KS D 6763 알루미늄 및 알루미늄 합금 봉 및 선
- KS D 3557 리벳용 원형강
- KS D 3698 냉간압연 스테인리스강판 및 강대
- KS D 8301 알루미늄 및 알루미늄합금의 양극 산화 피막
- KS D 8303 알루미늄 및 알루미늄 합금의 양극 산화 도장 복합 피막
- KS D 8312 알루미늄 및 알루미늄합금의 양극 산화 피막의 변형에 의한 균열 저항성 시험 방법
- KS D 8316 알루미늄 및 알루미늄합금의 양극 산화 피막의 내식성 시험방법
- KS Q 1001 계량규준형 1회 샘플링 검사
- KCS 14 31 00 강구조공사
- KCS 24 00 00 교량공사
- KCS 47 00 00 철도공사
- KDS 14 20 00 콘크리트구조 설계(강도설계법)
- KDS 24 00 00 교량 설계기준
- 토목공사 표준일반시방서
- ANSI/AWS D1.2/D1.2M Structural Welding Code-Aluminum, AWS
- LRFD Bridge Construction Specifications, AASHTO
- LRFD Bridge Design Specifications, AASHTO
- ASTM B221 Aluminum and Aluminum-Alloy Extruded Bars, Rods, Wire, Profiles, and Tubes
- ASTM B308/308M Aluminum-Alloy 6061-T6 Standard Structural Profiles
- ASTM B429 Aluminum-Alloy Extruded Structural Pipe and Tube
- ASTM B316/B316M Aluminum and Aluminum-Alloy Rivet and Cold-Heading Wire and Rods
- ASTM B26/B26M Aluminum-Alloy Sand Castings
- ASTM B108 Aluminum-Alloy Permanent Mold Castings
- ASTM F593 Stainless Steel Bolts, Hex Cap Screws, and Studs
- ASTM F594 Stainless Steel Nuts
- ASTM F606 Determining the Mechanical Properties of Externally and Internally Threaded Fasteners, Washers, Direct Tension Indicators, and Rivets
- AASHTO M 164 Structural Bolts, Steel, Heat Treated, 120/105 ksi Minimum Tensile Strength
- AASHTO M 291 Carbon and Alloy Steel Nuts
1.3 용어의 정의
- 가조임볼트: 부재의 가조립 또는 가설(설치) 시 연결부에 위치를 이음 고정하여 부재의 변형 등을 막기 위해서 임시로 사용하는 볼트
- 단조품: 흑피품이라고도 하며 단조성형된 채로의 형상인 것으로 형타단조품, 자유단조품, 중공단조품 등이 있고 단조작업 온도에 따라 열간단조품, 온간단조품, 냉간단조품이 있음.
- 단품 제작: 제작품의 중량, 설치 및 운송을 고려하여 일정 규모의 단일 부재로 제작하는 공정
- 뒷댐재: 맞대기 용접을 한 면으로만 실시하는 경우 충분한 용입을 확보하고 용융금속의 용락을 방지할 목적으로 동종 또는 이종의 금속판, 입상 플럭스, 불성 가스 등을 루트 뒷면에 받치는 것
- 브리넬경도: 강구압지를 사용하여 시험편에 구상의 압입자국을 만들었을 때의 하중을 압입자국의 직경으로부터 구한 압입자국의 표면적으로 나눈 값
- 비커스경도: 대면각 136°의 정사각뿔인 다이아몬드 압자를 일정한 시험하중으로 시료의 시험면에 압입하여, 생긴 영구오목부의 표면적으로 나눈 값
- 알루미늄 단조품: 단조품을 적당한 단련 성형비를 주도록 알루미늄괴 또는 알루미늄편을 단련성형하여 보통 소정의 기계적 성질을 주기 위하여 열처리를 시행한 것
- 알루미늄 주조품: 용해된 알루미늄을 주형에 주입하여 소요모양의 제품으로 한 것
- 엔드탭: 용접이 시작되거나 또는 종료되는 곳에 설치되는 별도의 재료
- 재편조립: 재단도에 의하여 절단한 판재나 형강 등을 조립하는 공정
1.4 제출물
1.4.1 일반사항
- 계약상대자는 제작 착수 전 알루미늄 구조부재의 제작, 조립, 설치 등에 관한 시공계획서를 제출하여 감독자의 승인을 받아야 한다. 시공계획서 내용에는 아래사항이 포함되어야 한다.
1.4.2 시공계획서 포함 사항
- 공정표 및 공정관리계획
- 상세 설계도서 검토
- 알루미늄재 구입 및 조달
- 제작(현도, 가공, 용접)
- 가조립
- 도장(공장도장, 현장도장)
- 수송계획
- 조립 및 가설
- 상부슬래브공
- 알루미늄재 구입 및 조달
- 알루미늄 판재 및 형상재
- 용접재료, 볼트 및 연결재 등
- 주조품 및 부속품 등
- 제작 및 제작관리
- 제작 시설용량 및 주요기기
- 제작도
- 용접 시공시험 계획서
- 용접 시공요령 및 절차서
- 용접 검사 및 절차서
- 제작품 검사 계획서
- 가조립
- 가조립 계획서
- 장비사용 계획서
- 가조립 시공요령 및 절차서
- 가조립 검사 계획서
- 도장계획(공장 및 현장도장)
- 도료사용 계획서
- 도장시공요령 및 절차서
- 도장검사 계획서
- 수송계획
- 조립 및 가설계획
- 조립 및 가설 계획도
- 가설 상세도
- 장비사용 계획서
- 부재연결 요령 및 절차서
- 조립 및 가설 요령 및 절차서
- 가설검사 계획서
- 시공검측 및 측량 계획서
- 품질관리계획(시험 및 검사계획)
- 알루미늄재류 및 부속품류
- 제작도 및 제작공정(현도, 절단, 용접 등)
- 용접공자격, 용접기자재, 용접절차
- 공장도장 및 현장도장
- 조립 및 가설
- 완성품검사
- 응력조정
- 시공검측 및 측량 계획
- 안전관리계획
- 안전관리 개요 및 계획
- 작업장 주변 안전관리 대책
- 공종별 안전관리 대책
- 추가사항
- 수급인은 수급인 및 제작자의 이름이 명기된 제작보고서 또는 시공보고서를 제출하여야 한다.
1.5 품질보증
1.5.1 알루미늄 구조부재 제작
- 알루미늄 구조부재는 공자감독자의 승인을 받은 알루미늄구조물 제작공장에서 제작한 것으로서 품질이 보증된 것을 사용하여야 한다.
- 알루미늄 구조부재 제작 공정과 제작 품질에 대해서는 사전에 시간을 두고 검사를 받을 수 있도록 검사조서를 의뢰하여 공사감독자의 승인을 받아야 한다.
- 이 시방서가 정한 제반규정 이외의 알루미늄 구조부재 제작 및 품질관리에 필요한 추가사항에 대해서는 해당 공사시방서 또는 수급인 및 제작자가 작성하여 공사감독자의 승인을 받은 절차서에 따른다.
- 가공 시 주요부재 및 2차 부재의 구분은 제작 전에 공사감독자의 승인을 받은 작업계획서에 따른다.
- 알루미늄 구조부재 제작 및 시공의 품질확보와 품질보증을 위하여 공사실명제를 실시하여야 한다. 제작 및 계약상대자는 해당공사의 시공작업 계획서, 품질관리 절차서 및 품질검사 절차에 따라 제작자 또는 수급인의 이름을 제작보고서 또는 시공보고서에 명기하여 제출하여야 한다.
2. 자재
2.1 일반사항
2.1.1 적용범위
- 이 장은 알루미늄 구조부재 제작에 사용되는 알루미늄재의 종류와 규격, 운반 및 저장 관리업무에 적용한다.
- 알루미늄재는 판재, 압출재, 주조품, 단조품, 볼트 및 연결재, 정착재, 주조품 등과 이들의 부속재료를 포함한다.
2.1.2 제출자료
- 수급인 및 제작자는 알루미늄재 구입 시 알루미늄재 제조공정, 시험 및 검사계획, 운송계획 등 알루미늄재 생산과 품질에 관련된 자료를 제출하여야 한다. 구입품별 제출자료는 표 2.1-1과 같다.
| 품명 | 자료 | |—|—| | 알루미늄재 | 재료의 밀시트 및 입고명세서 | | 고장력 볼트 | 재료의 밀시트, 세트의 검사 성적서 | | 볼트 및 앵커볼트 | 재료의 밀시트(일반볼트 제외), 볼트의 제품 검사 성적서 | | 스터드 | 재료의 밀시트 |
- 알루미늄재 및 부속품 구입품의 품질확인 및 검증을 위한 밀시트, 재료시험보고서, 제품 검사보고서 및 제품 검사성적서 등의 작성은 다음 중 해당 표준에 따른다.
- KS D 1851: 알루미늄 및 알루미늄 합금 분석 방법 통칙
- KS B 0802: 금속 재료 인장 시험 방법
- KS D 0242: 알루미늄 평판 접합 용접부의 방사선 투과 시험 방법
- KS D 1851: 알루미늄 및 알루미늄 합금 분석 방법 통칙
- KS D 1869: 알루미늄 및 알루미늄합금의 아연 분석 방법
- KS Q 1001: 계량규준형 1회 샘플링 검사
- KS에 등재되지 않는 알루미늄재는 알루미늄재 공급원별로 사용되는 최대 두께의 알루미늄재에 대해 해당 또는 동등 이상의 KS 또는 유사한 국제 기준에 따른 기본적인 요구성능의 검증을 입증할 수 있는 자료를 제출하여야 한다.
- 용접이음을 하는 알루미늄재는 모재에 대한 기본적인 요구성능에 대한 자료 이외에 용접부의 성능을 검증할 수 있는 자료를 제출하여야 한다.
2.1.3 품질보증
- 알루미늄재는 KS 인증 업체, 또는 공사감독자의 승인을 받은 공장에서 제조되어야 한다.
- 규격품 이외의 알루미늄재를 사용하고자 할 때는 사용알루미늄재의 해당 산업표준 절차에 의하여 제 시험에 합격한 품질확인서를 제출하여 감독자의 승인을 받아 사용할 수 있다.
2.1.4 운송 및 보관
- 알루미늄재의 운송, 보관 및 취급 시는 알루미늄재의 휨, 긁힘 및 과재응력은 피하여야 한다. 휘거나 손상을 입을 수 있는 내민 부분은 나무로 막거나 다른 방법으로 보호하여야 한다.
- 알루미늄재는 바닥, 먼지, 기름, 피복되지 않은 강재 등의 이물질과 접촉 되지 않도록 해야 한다. 지상의 마루, 받침목 또는 기타 지지물 위에 보관하고, 부식되지 않게 덮어서 보호하여야 한다.
2.2 종류 및 품질
2.2.1 알루미늄 판재
- 알루미늄 판재는 KS D 6701, KS D 6705, 또는 ASTM B209에 따른다.
| 산업표준 | 종류 | 기호 | 두께 (mm) | |—|—|—|—| | ASTM B209 (KS D 6701) | A 5083 P | H321 | 5 ≤ ≤ 40 | | ASTM B209 (KS D 6701) | A 5456 P | H116 | 5 ≤ ≤ 30 | | ASTM B209 또는 ASTM B221 | A 6061 P | T6 | 5 ≤ ≤ 6.5 | | ASTM B209 또는 ASTM B221 | A 6061 P | T651 | 6.5 ≤ ≤ 100 | | ASTM B209 | A 5086 P | H116 (H112-KS) | 6.5 ≤ ≤ 50 | | ASTM B221 | 6063 | T6 | 3 ≤ ≤ 25 |
주: 교량용 부재는 두께 5mm 이상의 두께를 갖는 알루미늄판을 사용하는 것이 좋다.
2.2.2 알루미늄 압출재
- 알루미늄 압출재는 KS D 6759, 또는 ASTM B221, ASTM B308/308M 또는 ASTM B429에 따른다.
2.2.3 알루미늄 단조품
- 알루미늄 단조품은 ASTM B247에 따른다.
- 알루미늄 단조품이 하중을 받는 구조재로 사용될 경우에는 실물크기 시험체에 대한 하중 재하시험을 통행 설계도서에서 요구하는 강도와 변형 용량을 확보 여부를 확인하여야 한다.
- 실물크기 하중재하시험의 빈도는 관련 KS 표준을 참조하여 정할 수 있다. 단, 동일 제품에 대한 제작사의 품질관리 실적이 있는 경우에는 공사감독자의 승인을 받아 시험의 빈도를 줄일 수 있다.
2.2.4 알루미늄 주조품
- 알루미늄 주조품은 ASTM B26/B26M에 따른다.
- 알루미늄 주조품이 하중을 받는 구조재로 사용될 경우에는 실물크기 시험체에 대한 하중 재하시험을 통행 설계도서에서 요구하는 강도와 변형 용량을 확보 여부를 확인하여야 한다.
- 실물크기 하중재하시험의 빈도는 관련 KS 표준을 참조하여 정할 수 있다. 단, 동일 제품에 대한 제작사의 품질관리 실적이 있는 경우에는 공사감독자의 승인을 받아 시험의 빈도를 줄일 수 있다.
2.2.5 알루미늄 리벳
- 알루미늄 리벳은 ASTM B316/B316M에 따른다.
2.2.6 알루미늄 전단연결재
- 전단연결재는 ANS/AWS D1.5/D1.2M에 따른다.
2.2.7 고장력볼트
- 구조용 알루미늄 접합용 고장력볼트는 KS B 1010, F8T에 따르며, 강재와 접하는 알루미늄재의 전식을 방지하기 위해 아연 도금한 것을 사용한다.
- 고장력볼트의 아연도금은 AASHTO M 232M/M 232 (ASTM A153/153M), Class C에 따라 용융아연도금을 하거나 AASHTO M 298 (ASTM B695)에 의거하여 기계적 도금을 실시하여야 한다. 볼트 세트를 이루는 와셔, 너트 및 볼트는 동일한 공정에 따른 아연도금을 하여야 한다. 이 때, 너트는 식별 가능한 염료를 포함한 윤활제로써 윤활 작업을 거치도록 하여, 설치 시에 윤활제에 대한 육안 검사가 이뤄질 수 있도록 한다.
2.2.8 스테인레스강 볼트
- 스테인레스강 볼트는 ASTM F593 Alloy Groups 1, 2, 3에 따르며, 너트는 ASTM F594에 따른다.
- 스테인레스 합금강 304와 316 볼트는 도금하지 않고 알루미늄 구조물에 직접 접촉된 상태로 사용할 수 있다.
3. 제작
3.1 알루미늄재 식별
- 밀성적보고서 등으로 식별할 수 있는 알루미늄재는 제작과정에 절단된 후에도 각각의 절단된 요소의 재질을 식별할 수 있도록 관리하여야 한다.
- 절단된 요소의 재질 식별을 위해 각 요소에 재질식별 번호를 표기하거나 표 3.1-1과 같은 색으로 표시할 수 있다. 조립 후 남게 되는 부분에 각인, 흠이 되는 선, 천공 등으로 식별하는 방법은 사용하여서는 안 된다.
| 알루미늄재 종류 | 색깔 | 색의 종류 | 기준색 | |—|—|—|—| | 5083 | 적색, 회색 | 5R 4/13, N 7.0 | N 9.5 | | 5086 | 적색, 연한황색 | 5R 4/13, 5.6Y 9.0/1.0 | | 6061 | 청색 | 3.4G 6.3/7.3 | | 6063 | 등황색 | 2.5YR 6/13 |
3.2 알루미늄 판재 가공
3.2.1 절단
- 설계도서에 별도로 명시되지 않은 경우 주부재 또는 플랜지 및 주 인장부재의 이음판으로 사용될 판재는 주응력 방향과 압연방향이 일치하도록 절단하여야 한다.
- 하중을 받는 두께 12mm 이상의 판재는 전단절단해서는 안 된다.
- 아크 절단한 모든 모서리는 모서리의 균열들을 모두 제거되도록 깎아내야 한다.
- 산소절단은 사용해서는 안 된다.
- 부재의 한 부분을 절단 제거한 곳은 곡률반경이 20mm 이상이어야 한다.
3.2.2 굽힘
- 용접하지 않은 하중을 받는 압연 알루미늄 판재의 굽힘 선은 압연방향에 직각이어야 한다.
- 굽힘 작업 전에 굽혀지는 구간의 판재 모서리는 곡률반경 1.6mm 이상으로 둥글게 해야 한다.
- 냉간굽힘은 균열을 유발해서는 안 된다.
- 90°냉간굽힘의 경우, 굽힘 내측면의 곡률반경은 표 3.2-1의 값 이상이어야 한다.
| 알루미늄 종류 | 판두께(mm) | 4.8 | 6.4 | 9.6 | 12.7 | |—|—|—|—|—|—| | 5083-H321 | 7.2 | 9.7 | 19.1 | 31.8 | | 5086-H116 | 7.2 | 12.7 | 23.9 | 38.1 | | 5456-H116 | 7.2 | 16.0 | 28.7 | 44.5 | | 6061-T6 | 14.3 | 22.4 | 43.0 | 63.5 |
3.3 보강재 부착
- 거더의 지점 보강재와 집중하중을 전달하기 위한 보강재는 하중이 잘 전달되도록 플랜지에 완전 지지되어야 한다. 여기서 완전지지는 기계가공, 그라인딩 등으로 정밀 가공하여 접촉면을 밀착시켜서 얻을 수 있으며, 플랜지가 압축력을 받는 구간에서는 용접할 수 있다.
- 집중하중을 전달하기 위한 보강재가 아닌 경우에는, 설계도서에 달리 명시되지 않은 한, 압축 플랜지에 밀착되도록 설치하여야 한다.
3.4 부재 단부 지압이음
- 트러스 또는 기둥의 압축력을 받는 부재의 맞대기음부에서 서로 맞대고 있는 부재 선단의 면에 작용하는 지압력에 의해 힘이 전달되는 경우, 서로 맞닿은 선단 면이 균일하게 지지되도록 각 부재의 선단을 기계가공, 톱절단 등을 하여야 한다.
3.5 지압면 가공
| 지압면의 경우 | 가공면의 품질 | |—|—| | 압축부재 선단의 기계 가공한 면, 기계가공 또는 그라인딩 한 보강재 또는 필러의 선단 면 | ANSI 12.5μm | | 롤러 또는 락커 받침의 필러 | ANSI 12.5μm | | 핀과 핀 구멍의 필러 | ANSI 12.5μm | | 미끄럼받침의 필러 | ANSI 12.5μm |
3.6 변형 교정
- 판재, 형상재, 조립 부재 등의 변형 교정은 금속에 어떤 손상이나 균열이 발생하지 않도록 하여야 한다.
- 뒤틀린 부재는 기계적인 방법이나 열간가공 교정에 의해 교정될 수 있다.
- 열처리 불가한 알루미늄재와 열처리 가능한 알루미늄재는 감도자의 승인을 받은 경우에만 정해진 절차에 따라서 열 교정을 할 수 있다. 가열 온도와 시간 등이 알루미늄재의 강도에 미치는 영향은 ANSI/AWS D1.2/D1.2M Structural Welding Code-Aluminum 등을 참조할 수 있다.
3.7 구멍 뚫기
3.7.1 일반사항
- 구멍뚫기는 다음 중 한 방법으로 한다.
- 드릴로 정확한 공칭 치수의 구멍을 뚫는다.
- 눌러뚫기로 공칭 치수보다 작은 초벌 구멍을 만든 후 공칭치수의 구멍이 되도록 리머 다듬질 한다.
- 드릴로 공칭 치수보다 작은 초벌 구멍을 만든 후 공칭치수의 구멍이 되도록 리머 다듬질 한다.
- 리머다듬질하기 전의 초벌 구멍의 치수는 구멍의 공칭치수보다 부재 두께의 1/4 또는 최소 0.8mm 이상 작아야 한다.
- 리머 다듬질 또는 드릴로 만든 구멍은 원형이며, 부재에 직각이어야 한다. 가공하면서 생긴 구멍 주변의 가시는 제거하여야 하며, 구멍의 직경은 공칭직경보다 0.8mm를 초과해서는 안 된다.
3.7.2 볼트군 구멍 정밀도
- 리머다듬질 전에 조립했을 때 인접한 볼트군의 구멍은 다음 두 조건을 만족하여야 한다.
- 구멍의 공칭직경보다 3.2mm 작은 원형 핀이 구멍의 확대 없이 부재 면에 직각인 방향으로 구멍 총 개수의 75% 이상의 경우에 관통하여야 한다.
- 구멍의 공칭직경보다 4.8mm 작은 원형 핀이 구멍의 확대 없이 부재 면에 직각인 방향으로 모든 구멍의 경우에 관통하여야 한다.
- 리머다듬질 또는 최종 치수로 드릴 천공 한 후에는 구멍 총 개수의 85% 경우에 서로 접합되는 두 부재 사이의 구멍 편차가 0.8mm를 초과하여서는 안 된다.
3.8 볼트구멍 위치잡기
- 볼트 구멍 작업을 위해 공장 또는 현장에서 부재를 조립할 수 있으며, 볼트구멍의 최종 위치잡기는 다음과 같은 방법 중에 선택하여 적용할 수 있다.
- 부재를 조립하지 않은 상태로 구멍을 눌러뚫기 또는 드릴로 초벌뚫기 하고, 조립하면서 구멍이 정확히 위치하도록 리머다듬질 한다.
- 형판을 사용하거나 또는 수치제어 방법으로 공칭치수의 구멍을 드릴로 뚫는다.
- 부재를 조립하면서 공칭치수의 구멍을 드릴로 뚫는다.
3.9 핀 및 롤러
3.9.1 일반사항
- 핀과 롤러는 도면에 명기한 치수에 맞추어 표면의 흠을 제거하고 평탄하고 매끄럽게 제작한다.
3.9.2 핀구멍의 허용오차
- 핀구멍의 직경은 핀의 공칭직경 보다 0.4mm를 초과하지 않아야 한다.
3.10 풀림 및 응력제거
- 볼트구멍 뚫기 작업은 모든 열처리 공정이 마무리된 후에 시행되어야 한다.
- 알루미늄 부재는 용접 후에 열처리 하여서는 안 된다.
3.11 알루미늄바닥판
3.11.1 일반사항
- 이 기준 3.11.2의 교량용 알루미늄바닥판 치수에 대한 허용오차는 각각 완성된, 그러나 하중재하 없는 상태의 패널에 대한 것이다.
- 제작오차 측정의 기준선은 알루미늄바닥판 패널의 작은 변의 1.5배 길이와 긴 변의 길이 중 작은 값을 초과하지 않는 길이의 곧은 선 또는 곡선(부재의 공칭 형상에 따라서)으로 하며, 측정 기준선의 양 끝 점이 부재와 접하도록 위치시킨다. 제작오차 측정의 기준선에서 측정된 두 점 사이의 거리가 각 공식에서 적용해야 하는 제원보다 작은 경우, 이 거리를 허용오차를 정하는 공식에 적용한다.
3.11.2 평탄도 및 직선도
- 평탄도는 알루미늄바닥판 블록 전체를 기준으로 하는 경우와 보강재 사이의 패널 크기를 기준으로 하는 경우가 있다. 패널의 평탄도는 최대편차가 다음 두 값 중 큰 값을 초과해서는 안 된다. 여기서, 패널은 U 리브 등 종방향보강재 사이와 횡방향보강재 사이의 순 면적부(clear area)를 뜻한다.
4.8(mm) 또는 (mm) (3.11-1)
- 여기서,
- : 패널 경계의 최소길이(mm)
- : 패널 강판의 최소두께(mm)
- 여기서,
- 압축력을 받는 종방향보강재의 직선도는 보강재 직각방향으로의 제작오차가 다음 값을 초과하여서는 안 된다.
≤(mm) (3.11-2)
- 여기서,
- : 종방향보강재의 제작오차를 측정하는 기준선의 길이(mm)
- 여기서,
- 웨브의 횡방향보강재와 압축력을 받지 않는 기타 보강재의 직선도는 보강재 직각방향으로의 제작오차가 다음 값을 초과하여서는 안 된다.
≤(mm) (3.11-3)
- 여기서,
- : 횡방향보강재의 제작오차를 측정하는 기준선의 길이(mm)
- 여기서,
3.11.3 공장가조립 검사
- 알루미늄바닥판 제작완료 후 제작검사는 전체크기에 대해 수행하며, 이때 검사에 필요한 시설, 장비, 인력, 재료 등은 수급인 또는 제작자가 준비한다.
- 제작검사 결과 알루미늄바닥판의 평탄도와 직선도가 허용오차를 초과할 경우는 감독자의 승인을 받아 수정 또는 보완 조치를 취한다.
3.12 부식 방지
3.12.1 일반사항
- 이 기준 2. 자재의 구조용 알루미늄재에 대해서는 다음