KCS 표준시방서 243110 용접(한계상태설계법)
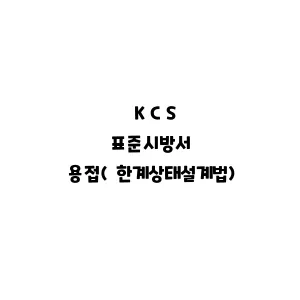
1. 일반사항
1.1 적용범위
- 이 기준은 도로교 설계기준에 따라 설계한 강도로교 및 기타 강구조물의 용접에 적용한다.
- 이 기준에 명시되지 않은 사항은 당해 공사의 공사 시방서에 따른다.
1.2 참고 기준
1.2.1 관련 법규
- 건설기술진흥법
1.2.2 관련 기준
- KS B 0052 용접기호
- KS B 0106 용접용어
- KS B 0529 머리붙이 스터드 용접부의 굽힘 시험 방법
- KS B 0801 금속재료 인장 시험편
- KS B 0802 금속재료 인장 시험방법
- KS B 0804 금속재료 굽힘 시험
- KS B 0805 브리넬 경도 시험방법
- KS B 0806 로크웰 경도 시험 방법
- KS B 0809 금속재료 충격 시험편
- KS B 0810 금속재료 충격 시험방법
- KS B 0811 금속재료 비커스 경도 시험방법
- KS B 0816 침투탐상 시험방법 및 지시모양의 분류
- KS B 0817 펄스에코법에 의한 금속재료의 초음파탐상검사에 대한 일반 규칙
- KS B 0821 용착금속의 인장 및 충격시험
- KS B 0825 아크용접이음의 한쪽인장 피로시험방법
- KS B 0826 용착금속의 경도시험방법
- KS B 0842 측면 필릿 용접이음의 전단 시험방법
- KS B 3500 T형 필릿 용접이음의 굽힘 시험방법
- KS B 0845 강용접 이음부의 방사선투과검사
- KS B 0867 겹치기 이음 용접 균열 시험 방법
- KS B 0872 C형 지그 구속 맞대기 용접 균열 시험방법
- KS B 0885 수동용접 기술검정의 시험 방법 및 판정기준
- KS B 0896 페라이트계 강 용접 이음부에 대한 초음파탐상검사
- KS B 0952 용접재료에 대한 기술적 인도 조건 — 제품 종류, 치수, 허용오차 및 표시
- KS B 1062 머리붙이 스터드
- KS B ISO 4136 금속용접부 파괴시험-횡방향 인장시험
- KS B ISO 5173 금속재료 용접부의 파괴시험 – 굽힘시험
- KS B ISO 5178 금속재료 용접부 파괴시험-용융용접부의 종방향 인장시험
- KS B ISO 9018 금속 재료 용접부의 파괴 시험-십자형 및 겹치기 이음 인장 시험
- KS B ISO 9712 비파괴검사-기술자의 자격인정 및 인증
- KS B ISO 13588 용접부의 비파괴검사-초음파 탐상검사-자동화된 위상배열 기술의 사용
- KS B ISO 14171 용접 재료 – 비합금과 세립강의 서브머지드 아크 용접용 솔리드 와이어 전극, 튜브형 코어드 전극 및 전극과 플럭스의 조합 – 분류
- KS B ISO 14174 용접 재료-서브머지드 아크 용접 및 일렉트로슬래그 용접용 플럭스-분류
- KS B ISO 14731 용접 업무 조절-임무와 책임
- KS B ISO 15614-1 금속재료 용접절차의 시방과 자격인정 – 용접절차시험 – 제1부: 강의 아크 및 가스 용접과 니켈과 니켈합금의 아크 용접
- KS B ISO 17642-2 금속재료 용접부의 파괴시험-용접부의 저온균열시험-아크 용접공정-제2부:자체구속형 시험
- KS B ISO 26304 용접 재료 – 고장력강의 서브머지드 아크 용접용 와이어 전극, 튜브 코어드 전극 및 전극 – 플럭스 조합 전극 – 분류
- KS D 0001 강재의 검사통칙
- KS D 0064 강 용접부의 수소량 측정 방법
- KS D 0210 강의 매크로 조직 시험방법
- KS D 0213 강자성 재료의 자분탐상검사 방법 및 자분 모양의 분류
- KS D 3503 일반 구조용 압연 강재
- KS D 3515 용접 구조용 압연 강재
- KS D 3529 용접 구조용 내후성 열간 압연 강재
- KS D 3542 고내후성 압연강재
- KS D 3558 일반구조용 용접 경량 H형강
- KS D 3868 교량구조용 압연강재
- KS D 7004 연강용 피복아크 용접봉
- KS D 7005 연강용 가스용접봉
- KS D 7006 고장력강용 피복아크 용접봉
- KS D 7023 저온용 강용 피복아크 용접봉
- KS D 7025 연강 및 고장력강용 마그 용접 솔리드 와이어
- KS D 7101 내후성강용 피복아크 용접봉
- KS D 7104 연강, 고장력강 및 저온용 강용아크 용접 플럭스 코어선
- KS D 7106 내후성 강용 탄산가스 아크용접 솔리드와이어
- KS D 7109 내후성 강용 탄산가스 아크용접 플럭스 코어드 와이어
- KCS 14 31 00 강구조공사
- KCS 47 00 00 철도공사
- KDS 24 00 00 교량 설계기준
- AWS D1.5 Bridge Welding Code, American Welding Society
1.3 용어의 정의
- 가붙임용접: 본용접 전에 용접되는 부재를 정해진 위치에 잠정적으로 유지시키기 위해 수행되는 비교적 짧은 길이로 된 용접
- 가스메탈아크용접: 외부에서 용융금속을 대기영향으로부터 보호하기 위하여 보호가스를 공급하면서 연속으로 공급되는 용가재를 사용하는 아크용접
- 가조임볼트: 부재의 가조립 또는 가설(설치) 시 연결부에 위치를 이음 고정하여 부재의 변형 등을 막기 위해서 임시로 사용하는 볼트
- 고장력강: 보통 인장강도 490MPa급 이상의 압연재로서 용접성, 노치인성 및 가공성이 우수한 강재
- 기공: 용융금속 중에 발생한 기포가 응고 시에 이탈하지 못하고 용접부 내에 잔류하여 생기는 공동. 기포의 성장속도보다 용융금속의 응고속도가 굉장히 빠르면 크기가 매우 작은 핀홀이, 약간 느리면 블로우홀 이 생성됨. 블로우홀 중에서 길고 좁은 형상의 기공을 웜홀이라고 함. 블로우홀이 비드의 표면까지 성장한 상태에서 응고가 완료되어 형성된 용접부 표면의 작은 구멍을 피트라고 함
- 단강품: 단조품을 적당한 단련 성형비를 주도록 강괴 또는 강편을 단련성형하여 보통 소정의 기계적 성질을 주기 위하여 열처리를 시행한 것
- 단조품: 흑피품이라고도 하며 단조성형된 채로의 형상인 것으로 형타단조품, 자유단조품, 중공단조품 등이 있고 단조작업 온도에 따라 열간단조품, 온간단조품, 냉간단조품이 있음
- 단품 제작: 제작품의 중량, 설치 및 운송을 고려하여 일정 규모의 단일 부재로 제작하는 공정
- 뒷댐재: 맞대기 용접을 한 면으로만 실시하는 경우 충분한 용입을 확보하고 용융금속의 용락을 방지할 목적으로 동종 또는 이종의 금속판, 입상 플럭스, 불활성 가스 등을 루트 뒷면에 받치는 것
- 백가우징: 용접루트부의 금속을 뒷면에서 가우징으로 제거하는 것을 말한다. 백가우징은 용접금속 또는 모재를 제거하여 후속 용접에서 건전한 용접부를 얻기 위해 실시한다.
- 브리넬경도: 강구압지를 사용하여 시험편에 구상의 압입자국을 만들었을 때의 하중을 압입자국의 직경으로부터 구한 압입자국의 표면적으로 나눈 값
- 비커스경도: 대면각 136°의 정사각뿔인 다이아몬드 압자를 일정한 시험하중으로 시료의 시험면에 압입하여, 생긴 영구오목부의 표면적으로 나눈 값
- 생산용접: 구조물에 실제 사용될 부재를 제작하기 위해 실시하는 용접
- 샤르피 충격시험: 샤르피 충격시험기를 사용하여 시험편에 충격하중을 가하여 재료의 취성, 인성을 측정하는 시험법
- 서브머지드아크용접: 입상의 플럭스 내에서 와이어와 모재 사이 또는 와이어끼리의 사이에 아크를 발생시켜 열로 실시하는 용접
- 스트롱백: 맞대기 용접 시에 이음판의 상호엇갈림 치수차를 수정함과 동시에 각변화를 방지하기 위해서 일시적으로 붙이는 보강재
- 스패터: 용접부의 일부를 이루지 않는 용융 용접 중 배출된 금속입자
- 아크에어가우징: 탄소봉을 전극으로하여 아크를 발생시켜 용융금속을 홀더의 구멍으로부터 탄소봉과 평행으로 분출하는 압축공기로서 계속 불어내어 홈을 파는 방법
- 언더매칭용접: 모재의 강도보다 낮은 강도의 용가재를 사용하는 용접
- 엔드탭: 용접이 시작되거나 또는 종료되는 곳에 설치되는 별도의 재료
- 용락: 용접금속이 홈의 뒷면에 녹아내리는 현상. 박판용접에 봉 용극을 사용하거나 용접하여야 될 판두께가 용융금속을 지탱할 수 있을 만큼의 루트면 치수가 없을 경우 또는 루트간격이 너무 클 경우 발생하는 현상
- 용접부 표준상세: 용접 실무에서 일반적으로 많이 적용하고 있는 용접부 상세로서 이 기준 부록과 같다. 이 외에 국내외의 관련 기준에 등록된 용접부 상세도 포함할 수 있음
- 용접시험판: 용접부에 대한 각종 시험편을 제작하기 위하여 용접한 강판
- 용접절차서(WPS): 용접부의 소요 품질을 확보하기 위하여 필요한 용접관련 정보를 기록한 명세서. 일반적으로 모재, 용접법, 용접상세, 용접자세, 용가재, 용접 전류 및 전압, 용접속도 등에 대한 정보를 포함하고 있음
- 용접절차검증시험: 제 3자에 의하여 제공된 PQR을 검증하기 위하여 수행하는 단순화한 시험
- 용접절차사전시험: 도급자가 WPS를 작성하기 위한 기초 자료로 사용하는 제 3자에 의한 WPS 인정시험
- 용접절차인정기록(PQR): WPS를 승인받기 위하여 시험한 내용을 기록한 서류. WPS 인정 시험편의 제작에 적용한 용접조건과 시험 결과의 실제 값이 포함되어 있음.
- 용접절차인정 시험(PQT): WPS를 승인받기 위하여 용접부에 대하여 실시하는 각종 시험.
- 저온균열: 약 200℃ 이하의 저온에서 발생하는 균열로 저온균열에는 루트균열, 토우균열, 비드하부균열 등이 있음
- 층분할방식: 용접층이 두꺼울 경우 단일층의 용접으로 시행하지 못하고 여러 층으로 나누어 용접을 시행하는 방법
- 케스케이드법: 다층 용접을 할 경우 각 비드의 일부를 인접 비드위에 겹쳐 용착하는 방법
- 코킹: 불연속을 밀폐 시키거나 또는 감추기 위하여 기계적인 방법으로 용접부나 모재의 표면에 소성변형을 가하는 작업
- 크레이터: 용접 비드가 끝나는 곳에 있는 함몰 자국
- 플럭스코어드아크용접: 코어드 와이어나 플럭스코어드 와이어 용접봉을 사용하는 용접
- 피닝: 충격타를 가하여 금속을 기계적으로 가공하는 작업
- 피복아크 용접: 용접하려는 모재표면과 피복 아크용접봉의 선단과의 사이에 발생하는 아크열에 의하여 모재의 일부를 용융함과 동시에 용접봉에서 녹은 용융금속에 의하여 결합하는 용접 방법
- 합금플럭스: 용접금속의 화학성분 조성을 변경하기 위하여 합금 원소를 함유하고 있는 플럭스. 용접전압의 변경은 용접금속의 화학성분 함유량에 심각한 변화를 초래할 수 있음
- 활성플럭스: 소량의 마그네시움, 또는 실리시움, 또는 두 성분을 함유하고 있는 플럭스로서, 단일패스 적용에서 용접을 개선하기 위하여 사용됨. 용접전압, 또는 용접패스의 개수의 변경은 용접금속의 화학성분 함유량과 역학적 성질에 심각한 변화를 초래할 수 있음
1.4 제출물
1.4.1 작업절차서
- 수급인은 용접시공에 앞서 용접방법과 용접절차서(WPS), 용접품질 검사방법 및 절차서를 작성하여야 한다.
- 용접절차서(WPS) 및 용접절차인정기록(PQR) 작성에 필요한 용접기호 및 용접용어는 KS B 0052 및 KS B 0106에 따른다.
1.4.2 용접 기술인력 자료
- 용접에 관련된 각 기술인력에 대한 자료를 신분증 사본과 함께 제출하여야 한다.
1.4.3 용접시공 기록 및 자료
- 제작이 완료되면 수습인은 용접재료, 용접시공 및 용접검사에 관한 기록을 제출하여야 한다. 용접검사 기록은 KS B 0816, KS B 0845, KS B 0896, KS D 0213, KS B ISO 13588 중 해당 표준에 따라 작성하여야 한다.
- 현장용접이 허용된 경우에는 현장용접 기기에 대한 명세서와 용접시공 기록을 작성하여 제출하여야 한다.
1.4.4 제작확인서
- 수급인은 제작이 완료되면 이 시방서에서 규정한 재시험과 KS에 따른 모든 시험과 분석에 대한 자료 및 용접시공에 관한 실명 날인한 보고서의 사본을 제출하여야 한다.
- 제작완료보고서에는 (1) 이외에 부재의 변형교정, 응력제거 방법 및 내용, 용접결함 보수사항 및 현장 품질관리기록을 포함한다.
1.5 품질보증
1.5.1 제작기기의 승인
- 강교제작을 위한 용접에 필요한 주요시설 및 기기 등은 사전에 공사감독자에게 승인을 받아야 한다.
- 다만, 건설기술진흥법 제58조 3항 및 시행령 제96조의 규정에 따라 인증된 해당 등급에 적합한 강구조물 제작공장인 경우에는 공사감독자의 사전승인을 생략할 수 있다.
1.5.2 용접절차서(WPS) 및 용접절차인정기록(PQR)
- 수급인은 용접시공에 필요한 모든 용접법에 대해서 용접절차서(welding procedure specification, 이하 WPS)와 용접절차인정기록(procedure qualification record, 이하 PQR)을 작성하고, 이를 보관하여야 한다.
- WPS의 인정과 관련된 사항은 이 기준 4. 인정에 따른다.
1.5.3 품질관리시험
- 제작자는 이 기준 4. 인정에 따라 WPS 인정을 받기 위한 시험 이외의 추가 용접시험이 필요할 경우 공사감독자의 승인을 받아 다음 중 해당시험을 실시하여야 한다.
- 용착금속의 인장 및 충격시험 : KS B 0821
- 아크용접 이음의 한쪽 인장피로시험 : KS B 0825
- 용착금속의 경도시험 : KS B 0826
- 금속재료 용접부의 파괴시험-금속 재료 용접부의 파괴 시험-십자 및 겹치기 이음 인장 시험 : KS B ISO 9018
- 측면 필릿 용접이음의 전단 시험 방법 : KS B 0842
- T형 필릿 용접이음의 굽힘 시험 방법 : KS B 3500
- 강 용접부의 수소량 측정 방법 : KS D 0064
- 부재 구조상세에 대한 피로 관련 시험은 제작과정에 특별한 문제가 있거나 별도의 규정이 있는 경우에만 실시한다.
1.5.4 완전용입 맞대기 용접부의 피로시험
- 완전용입 맞대기 용접부의 피로성능에 대한 평가 실적이 없는 공급원이 공급한 재료(모재, 용접봉 또는 와이어, 플럭스)를 사용하는 경우에는 용접부 인장 시험체에 대해 다음의 피로시험법에 따라 피로시험을 수행하고 그 합격 여부를 판단한다.
- 시험체의 용접철구제작공장 또는 공사현장 작업조건과 동일하거나 그보다 가혹한 조건에서 피로 성능평가용 시험체를 용접한다.
- 판두께별 시험체의 형상
- 시험체의 단면 폭(b)은 판두께(t)의 1.5배 이상으로 설정한다.
- 그립부 폭(w)이 단면 폭(b)의 1.5배 이상으로 설정한다.
- 시험체의 단면 평행길이(l)은 판두께(t)의 3배 이상으로 설정한다.
- 변화부 반경은 단면 폭(b)의 2.5배 이상 또는 구조해석을 통해 응력집중도(=변화부 응력/시험단면 응력)가 1.1 이하가 되도록 설정한다. 표 1.5-1은 판두께 별 피로시험체의 크기와 형상에 대한 예시이다.
| 판두께 (t) | 그립부폭 (w) | 단면폭 (b) | 평행부 길이 (l) | 변화부 반경 | 그립부 길이 | 시험체 총길이 | |—|—|—|—|—|—|—| | 20 | 90 | 40 | 170 | 100 | 250 | 802 | | 40 | 100 | 60 | 200 | 160 | 250 | 855 | | 60 | 140 | 90 | 250 | 240 | 250 | 963 | | 80 | 190 | 120 | 350 | 320 | 250 | 1,141 |
- 시험체의 정합도 평가
- 하중 축과 편심에 의한 시험체에 발생한 휨 변형율을 축방향 변형율로 나눈 값이 5% 이내 임을 정적 재하시험을 통해 확인 후 피로시험을 수행한다.
- 피로 시험체의 개수 및 시험조건
- 피로 시험체의 개수는 최소 9개 이상으로 하며, 3개의 피로하중 응력범위에 대하여 각각 3개씩 실험한다.
- 반복횟수 50만회 이상에서 피로파단이 일어나도록 피로하중 응력범위를 설정하되, 피로수명 200만회에 해당하는 피로강도 이하의 값이 포함되도록 한다. 이는 표 1.5-2의 판두께 별 피로하중의 크기와 응력범위에 대한 예시를 참조하여 적절히 정한다.
- 작용하중의 응력비는 0.05 이상으로 한다.
| 판두께 (mm) | 순단면적 (m2) | 최대하중 (kN) | 최소하중 (kN) | 최대응력 (MPa) | 최소응력 (MPa) | 응력범위 (MPa) | |—|—|—|—|—|—|—| | 20 | 0.0008 | 98 | 9.8 | 122 | 12.0 | 110.0 | | | | 123 | 12.3 | 153 | 15.5 | 137.5 | | | | 147 | 14.7 | 183 | 18.0 | 165.0 | | 40 | 0.0024 | 293 | 29.3 | 122 | 12.0 | 110.0 | | | | 366 | 36.6 | 153 | 15.5 | 137.5 | | | | 439 | 43.9 | 183 | 18.0 | 165.0 | | 60 | 0.0054 | 659 | 65.9 | 122 | 12.0 | 110.0 | | | | 824 | 82.4 | 153 | 15.5 | 137.5 | | | | 989 | 98.9 | 183 | 18.0 | 165.0 | | 80 | 0.0096 | 1,167 | 116.7 | 122 | 12.0 | 110.0 | | | | 1,462 | 146.2 | 153 | 15.5 | 137.5 | | | | 1,756 | 175.6 | 183 | 18.0 | 165.0 |
- 피로 시험결과의 판정
- 모든 피로 시험체가 도로교설계기준에 규정된 설계 피로등급의 피로강도 이상일 경우 합격한 것으로 한다.
- 재시험
- 불합격의 경우 같은 방법으로 1차로 재시험을 수행하여 모든 피로 시험체가 설계 피로등급의 피로강도 이상일 경우 합격한 것으로 한다.
- 1차 재시험이 불합격된 경우에는 (5)에 따라 2차 재시험을 수행하여, 하한 5% 피로강도 곡선이 설계 피로등급의 피로강도 이상일 경우 합격한 것으로 한다.
- 피로성능 평가 실적 유효성
- 사용하고자 하는 강재에 대한 피로 성능 평가 실적이 있더라도, 제강사(mill), 강종, 용접재료가 기존 실적자료와 다른 경우에는 해당 부재에 대한 피로성능 평가를 별도로 실시하여야 한다.
- 강종과 용접재료가 동일하더라도 최대 판두께, 개선형상, 용접자세, 최대 입열량, 최소 예열온도, 용접 비드 개선 등이 다른 경우에는 해당 공사에서 발생할 수 있는 가장 불리한 조건을 기준으로 피로 성능 평가의 추가 실시 여부를 공사감독자가 판단한다.
1.6 기술인력
1.6.1 용접사의 자격
- 용접사의 자격은 다음 중 하나에 해당하는 경우에 인정한다.
- KS B 0885 등 관련 한국산업표준의 해당요건에 따라 자격을 갖춘 자.
- 해당 작업에 2년 이상 경험이 있는 자로서 작업 투입 당시 해당 용접에 대하여 숙련된 기량을 갖고 있고, 제작사 자체 용접사 인정시험에 합격된 자.
- 이 기준 4.3에 따라 자격인정을 받은 자.
- 이 기준 4.2.8에 따른 입열량 인정에 합격한 용접시험판을 용접한 자. 이 용접사는 해당 용접법과 용접자세로 수행하는 그루브용접, 필릿용접, 슬롯용접에 대해서 자격이 인정된다. 인정되는 부재의 두께는 이 기준 표 4.3-2에 따른다.
- 국가기술자격법에 따라 자격증을 취득한 자.
- 수급인 또는 제작자는 공사에 참여하는 용접사의 신분증과 자격증의 사본을 제출받아 보관하고, 공사감독자가 확인할 수 있도록 하여야 한다.
1.6.2 용접업무 조정담당자
- 용접업무 조정담당자는 용접이나 용접 관련 업무에 관한 생산작업을 책임지며, 교육과 훈련 및 경험 등을 통하여 지식과 능력이 입증된 사람으로 한다. 용접업무 조정담당자의 기술적 지식은 KS B ISO 14731에 따른다.
- 용접업무 조정담당자의 업무 내역은 KS B ISO 14731에 따르며, 계약, 설계검토, 모재 및 소모품, 하청계약, 생산계획, 장비, 용접작업, 시험, 용접 승인, 문서화 등의 활동에 관련된 명세 또는 준비, 업무조절, 통제관리, 검사 및 점검 또는 입회의 임무와 책임을 포함한다.
- 용접업무 조정담당자는 하나 또는 다수의 업무조절과제를 수행한다. 다수에 의하여 용접업무가 조절되는 경우 각 개인에게 임무와 책임을 배정한다.
- 제작자는 적어도 1명 이상의 공인된 또는 공사감독자의 승인을 받은 용접업무 조정담당자를 임명한다.
1.6.3 비파괴검사 검사자
- 제작자 자체 품질관리의 일환으로 시행하는 검사는 최소 5년 이상 경력자로서 제작자가 선임한 해당 종목의 비파괴검사 기술자가 수행하여야 한다.
- 비파괴검사를 수행하는 검사자는 비파괴검사 기술의 진흥 및 관리에 관한 법률에 따라 국가기술 자격법 또는 KS B ISO 9712, 레벨 2 이상의 해당 종목 자격을 취득한 비파괴검사 기술자이어야 한다.
2. 용접재료
2.1 일반사항
2.1.1 적용범위
- 이 장은 용접에 사용되는 용접재료의 규격, 운반 및 저장 관리업무에 적용 한다.
- 용접재료는 용접봉, 플럭스, 스터드 등과 이들의 부속재료를 포함한다.
2.2 용접봉 및 플럭스
- 용접봉 및 플럭스는 KCS 14 31 20 (2.1)에 따른다.
2.3 스터드형 전단연결재
- 스터드형 전단연결재는 KCS 14 31 20 (2.2)에 따른다.
2.4 품질관리
- 용접재료의 품질관리는 KCS 14 31 20 (2.3)에 따른다.
3. 용접시공
3.1 공통사항
3.1.1 용접부 준비
- 용접을 하려는 부분의 재편조립 정밀도는 KCS 24 31 05(3.9)의 해당 규정에 따른다.
- 용접을 하려는 부분에는 기공이나 균열을 발생시킬 염려가 있는 흑피(黑皮), 녹, 도료, 기름 등이 있어서는 안 된다. 잘 제거되지 않는 흑피, 얇은 녹 방지용 코팅, 스패터 방지막 등은 남아 있을 수 있다.
- 재편에 수분이 있는 상태로 용접을 하여서는 안 된다. 재편에 수분이 있거나 입열 시 결로가 생길 우려가 있는 경우에는 용접선 부근을 건조시켜야 한다.
3.1.2 용접재료 선택 및 주의사항
- 사용하는 용접재료는 이 기준 2. 용접재료의 규정에 따른다.
- 피복아크 용접봉 및 플럭스는 사용에 앞서 건조로에서 건조한 상태에서 사용하여야 한다.
- 피복아크 용접봉은 피복재가 벗겨지거나 나쁜 상태로 손상된 것을 사용하여서는 안 된다.
- 용접봉의 적열(赤熱)이 발생되지 않도록 사용에 주의하여야 한다.
- 피복아크용접의 용접봉에 대해 다음 규정을 적용한다.
- 저수소계 용접봉을 사용하며, KS B ISO 17642-2 등으로 용접성능이 입증된 경우에는 다른 용접봉을 사용할 수 있다.
- 피복아크용접봉은 피복제가 오염되거나 손상 입은 것을 사용해서는 안 된다.
- 탄소강 피복아크용접봉은 밀폐용기에 포장된 것이거나 용접봉 제조사의 설명서에 따라 건조한 것을 사용하여야 한다.
- 저합금강 피복아크용접봉은 밀폐용기에 포장된 것이거나 370℃~425℃에서 1시간 이상 건조한 것을 사용하여야 한다.
- 용접봉은 밀폐용기를 개봉한 경우 또는 건조로에서 꺼낸 경우에는 즉시 120℃ 이상의 온도를 유지하는 오븐에 보관하여야 한다.
- 밀폐용기, 또는 건조로나 보관용 오븐에서 꺼낸 용접봉은 표 3.1-1의 허용시간 이내에 사용하여야 한다. 허용시간에 사용하지 못한 용접봉은 1회에